Note – small gas turbine power plants and turbine-powered gas pipeline compressing stations have been around for decades. A government/industry collaboration to advance gas turbine technology bore fruit in the late 1990’s. This started a massive building boom in large, highly efficient gas turbine plants.
I started looking around, and eventually was offered a position at a large (1048 Megawatt) facility that was then under construction. I went from burning dirt to operating one of the newest and most advanced gas turbines on the planet :) Fortunately it wasn't too difficult of a change, and being fully automated, it was not as challenging as the coal-burner to operate. I also learned that while gas turbine combustion and control logic are exceedingly complicated, the principle of operation is ridiculously simple. While the principle has been understood for a long time, it's only since WWII that practical gas turbines were actually built.
So how does a gas turbine work? As with coal furnaces, there are two major types that differ significantly from one another, although they both use the same principle, the Brayton Cycle.
Below is a diagram showing the four stages of combustion, both for a piston engine (the otto cycle) and a gas turbine (the brayton cycle). The similarities are that air is compressed, fuel is added and ignited, and work is derived from the expansion of the heated gases. The difference is that the piston engine delivers intermittent power, while the gas turbine compresses, burns, and delivers power continuously.
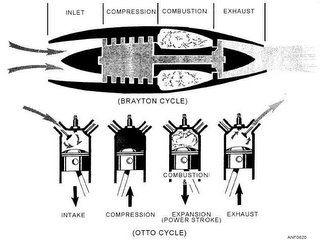
One footnote about the diagram: Most gas turbines used in power generation are not optimized to produce thrust (with one exception that I'm aware of), instead the turbine rotor will have an output shaft that spins at 3600 RPM, turning a generator.
The two types of gas turbines are calle aeroderivative and industrial. It's somewhat self-descriptive, except for the engineering finesse on each design. Aeroderivative engines are gas turbines originally designed for aircraft - they are light, high-revving, easily replaceable machines. In contrast, industrial gas turbines are heavy behemoths that turn at 3600 RPM and are not intended to be removed.
The simpler design, the industrial (or frame) engine, has a single shaft that has an axial compressor at one end, a combustion zone in the center, and a turbine at the exit end. How does it work? The compressor pulls in an enormous mass of filtered air and compresses it. Next, fuel is precisely metered and pre-mixed with the compressed air, and burned in a continuous process. The superheated air expands with great force trough several stages of turbine blades, which convert the expanding gas energy into rotational energy. Because the compressor and turbine are on the same shaft, the turbine provides the energy to drive the compressor, plus has extra power left over to run a generator. The shells on industrial turbines tend to be a couple of inches thick, so that a catastrophic failure will typically be contained within the shell.
In the aeroderivative design there are two rotors. One rotor is high-speed, typically operating at 9500-9700 RPM. This section contains the compressor, combustion zone and a high speed turbine to drive the compressor. In the exhaust path right behind the high speed turbine is a 'power turbine'. The power turbine is connected to a generator that turns at 3600 RPM. As the high speed turbine revs and generates more exhaust gas, the power turbine places more load on the generator. Failures on aeroderivative engines tend to be spectacular - the shells of the engines are light, being designed for aircraft, and when the high speed turbines fail, the blades are thrown at high velocity. Pieces of these turbines are often found outside their protective enclosures following a failure.
The current power plant design is called a "combined cycle" arrangement. In this case we have one or more gas turbines (Brayton Cycle) that operate a generator. The still-hot exhaust gas is then directed into a boiler to create steam and operate a steam turbine (Rankine cycle), increasing power output for the same quantity of fuel burned. Thus we combine cycles! Coupling the cycles yields efficiencies close to 60%. Coal burners and nukes run 30-35% if I recall correctly. Advanced simple cycle (stand alone) gas turbines hit about 40% efficiency.
4 comments:
'Most gas turbines used in power generation are not optimized to produce thrust (with one exception that I'm aware of'
A decade late I know, however, what is the exception? My first thoughts turned to an APU however I'm certain that isn't correct.
The FT8 Twinpac power plant uses a pair of Pratt-Whitney jet engines as gas generators that exhaust at opposite tangents into an expander. It's really a pretty slick arrangement, because if an engine craps out, no alignment of the replacement is necessary. Just pull the fuel and electrical, uncouple the ductwork, and pull it! Replacement is the reverse.
Brilliant. What additional containment is required in case of turbine failure?
Btw, I will be going through your posts year by year over the coming months because I think this blog is brilliant. Expect random comments here and there.
Re: Containment in event of turbine failure for the FT8 package... I'm pretty sure the stucture that the engine is installed in can contain a failure. The interior is about 6" thick accoustic-absorbing material, held in place with sheets of perforated stainless steel. The exterior is heavy-gauge steel paneling. Robust enough, I'd think, to contain a catastrophic failure.
Thank you for your kind words about the blog. I'm not sure "brilliant" is the right word. Maybe "clever" :) LOL.
Post a Comment