Below: The boiler structure of the Argus Cogeneration Expansion (ACE Project)
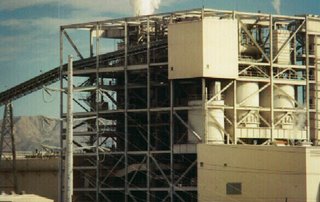
After a too-long stint at the robust but very simple and boring geothermal plant, I worked at a coal-fired cogeneration plant for a while. This was my only experience with a solid fuel-fired boiler and a hideously complex controlled-extraction steam turbine. Don't let anyone kid you - cogeneration plants that ship steam to sensitive industrial processes are *way* more complex than enormous stand-alone power plants!
Most large coal-fired utility boilers (350 Megawatts and up) use pulverized coal. Wiki has a pretty good explanation of how such boilers work. Essentially the coal is ground up into black flour and transported into the boiler in a stream of hot air, where it ignites like gasoline. In the center of such boilers is a fireball so intense that you need welding goggles to look at it. The disadvantages of burning coal in this manner are twofold: The intense heat generates large amounts of nitrous oxides (NOx), and it's impossible to control the formation of sulfur dioxide (an acid rain precursor), which results from the natural sulfur content of coal.
The facility I worked at used a CFB (Circulating Fluidized Bed) boiler however.
The combustion process occurs at about 1600 degrees F, rather than the 2400-2600 degrees in the pulverized coal process. This greatly reduces NOx formation. Furthermore, in this process limestone is added to the furnace. At this lower temperature it reacts with the sulfur present in coal to form Calcium Sulfate, aka gypsum, the material in drywall board. Definitely a more useful substance than acid rain :)
OK, so how does a CFB differ from a PC (pulverized coal) boiler? I'll explain the combustion air path for both, which should mostly describe the differences.
In a PC boiler, air is drawn in through a Primary Air fan, sent through a rotary regenerative heater, and then on to the coal pulverizers. The pulverizers have ground the coal to fine dust, which is picked up and transported along with the air into the furnace where it burns. The radiant heat from the combustion heats the walls of the boiler which are made of tubes containing water. The water becomes steam to turn a turbine...
Below is a photo of a single burner firing at a *very* low intensity inside a PC boiler. A typical large utility boiler will have 16-20 burners, burning an incredible 100 tons per hour of coal!
In the photo you can clearly see that:
1. The coal is burning rapidly, almost like a liquid
2. The walls of the boiler are made from numerous tubes welded together to form a wall
3. Slag has deposited on the walls of the boiler - at the lower left in the photo, the tubes look 'fuzzy'. This is slag.

The bottom of a PC boiler is... a water trough. Weird, eh? There's a good reason however. All boilers run at a negative internal pressure, so that any leaks will be air leaking in, rather than fire leaking out! Due to the high temperatures involved, minerals present in the coal melt and condense on surfaces inside the boiler. These condensed blobs of fused ash are called "slag" or "clinkers", and they grow larger and larger. Eventually they fall under their own weight to the bottom of the boiler. They are often quite large, and fall a long way (sometimes 10-15 stories, depending on the size of the boiler!). So how can we get them out while still keeping the boiler at a negative pressure and on line? Let them fall into the water and grind them up! Afterwards we can pump out the sludge with a fast-moving jet of water. This stuff is called the bottom ash.
Back to the fire though. The hot combustion gases have to go somewhere. A huge Induced Draft fan pulls the back end of the boiler and keeps the entire boiler at a negative pressure. This draft pulls the combustion gases up, past superheaters. This heats the steam beyond the temperature it was created at, adding to efficiency. The combustion gas then passes down the backpass, where it pre-heats water that is about to enter the boiler, also increasing efficiency. The still hot combustion gas passes through the hot side of the rotary regenerative heater and into (typically) an electrostatic precipitator.
The electrostatic precipitator removes fly ash that was carried away in the draft. The precipitator works by passing the ash-laden gas through a series of high-voltage plates that place a negative charge on the ash particles suspended in the gas. Next the gas passes into a region where there are positively charged plates. The negatively charged ash is attracted to the positively charged plates, and sticks to them. A shaker knocks the accumulated ash from the collection plates from time to time, and the ash falls into a hopper for later removal.
Urea is typically added at this point in order to reduce NOx. Another retro-fit after the precipitator is usually a wet scrubber. Here the stack gas passes through a circulating limestone slurry that absorbs most of the sulfur. The cleaned gas now passes through the Induced Draft fan and out the stack. The steam plume coming from stacks of large coal-fired plants is an indication the hot gases are evaporating steam from the wet scrubber. It's not harmful and it's cleaner than sulfur-laden combustion gas :) Whew!
On a CFB, things work a little differently though. Here is a diagram of how it works:

The air flow path is different here: Air is drawn in through a primary air fan once again, but this time goes through tubular air preheaters in the backpass. The primary air, now at 420 degrees F is blown into a grid at the bottom of the boiler. The purpose of the grid is to distribute the air and suspend the coal off the floor of the boiler. This is the "fluidized bed", a blend of ash, chunks of coal and granulated limestone. Underneath the fluidized bed, there is positive air pressure, yet throughout the remainder of the boiler pressure is negative.
The combustion process occurs at a much lower temperature than a PC boiler, and it's operationally also a bit sloppier as well. Through the viewport, it looks like a large pool of red-hot lava sloshing around, with the odd firefly of burning coal being sucked up along with the draft. Again, this heat is transferred to tubes in the walls of the furnace to make steam, and as with the PC boiler there is an Induced Draft fan pulling from the back.
Because the coal and ash bed is "fluidized", and because of the airflow from underneath, the bed stratifies a bit. Larger, heavier materials tend to stay near the bottom of the bed, while lighter particles are lofted completely out of the bed by the powerful draft, still on fire! For this process to be efficient, this lost fuel must be recovered and burned. To recpture these unburned particles, very large cyclone separators are used. The combustion gases and particulates go into a cyclone (or several) and are swirled, losing velocity. The combustion gas and minute flyash particles have little mass, so they pass to the center and exit the top. The heavier particles are flung to the outside and fall into return legs that drop them back into the bottom of the furnace for further combustion.
As on the PC boiler, the exhaust gas drops down through the backpass, superheating steam and preheating feedwater for the boiler. Then it goes into a "baghouse" or fabric filter (similar in operation to the bag your vacuum cleaner sports), to remove the flyash. The particle-free combustion gas then enters the the Induced Draft fan, then up and out the stack. Whew again.
The thing about working at the coal burner was how very physical it was. Something was *always* going wrong and spilling a lot of material. If there wasn't an ash leak at the baghouse, there was an ash leak in one of the transport lines. If not that, there would be a coal spill. If no coal spill, the limestone crusher or conveyor belt would dump a couple of tons of limestone. In addition to repairing the problem, you'd have a huge mess to clean up. Then too the control room could be a handful, particularly when something went wrong.
An additional level of complexity was added due to being a cogeneration facility. The steam turbine was able to force half-spent steam out of an extraction point and send it to the thermal host. It was always a tricky process, as this steam was robbed from the places it normally went in the plant - feedwater heaters and the Deaerator.
This facility received large quantities of condensate back from the thermal host - at the wrong temperature and chemistry for the boiler. There was a complex (and failure prone) cooling and treatment system to correct the problems with the returning water.
Coal-fired CFBs are very prone to tube failures, because the ash in the fluidized bed continuously erodes the water wall tubes. The huge airflows required to fluidize several tons of material create turbulence and eddys that contain fine abrasive ash particles. Eventually the ash wears a hole in a tube, and then the furnace must be shut down for repairs. I worked *a lot* of overtime there - a typical year would require 600 hours of overtime per employee.
One thing I liked about this facility though was the culture. We were encouraged to be involved in environmental reporting, maintenance, the chemistry program, and heavily involved in safety. Good thing with the safety program, too. There was a lot of dangerous stuff there - red hot ash, heights, conveyors, coal and ash dust, you name it. It was quite a challenging plant to operate at times - both physically and mentally.
Eventually though, it was time to leave, because a new wave of power plants was being built. Gas turbines!
A final word on CFB furnaces: They are very fuel flexible. A PC furnace can only burn high-quality, low ash coal. A CFB can burn anything solid that will burn - tires, agricultural waste, or coal-mining waste. In this sense CFB furnaces have been providing many eastern coal-mining communities with a valuable service: Eliminating huge watershed-polluting mountains of mine waste while generating electricity from them. A clear-cut case of win-win.
Here's a pitch someone wrote up for burning waste coal.
Here's a plant that accomplishes the process.
And... in the interest of equal time for opposing views, here's a link to an environmental group opposed to burning waste coal (with some seemingly valid reasons). They propose remediation by bringing in non-native grasses that readily grow in coal waste. Could they get out of hand spread, crowding out native vegetation? I dunno! Legacy waste is a pain in the neck, ain't it?
No comments:
Post a Comment